Accurate water pressure readings are crucial in various applications, including plumbing, irrigation, and industrial systems. Misleading readings caused by inaccurate gauges can lead to inefficiencies, potential damage to equipment, and even safety hazards, underscoring the importance of precise measurements. A water pressure gauge that hasn’t been calibrated properly may provide unreliable data, resulting in poor performance or unexpected system failures.
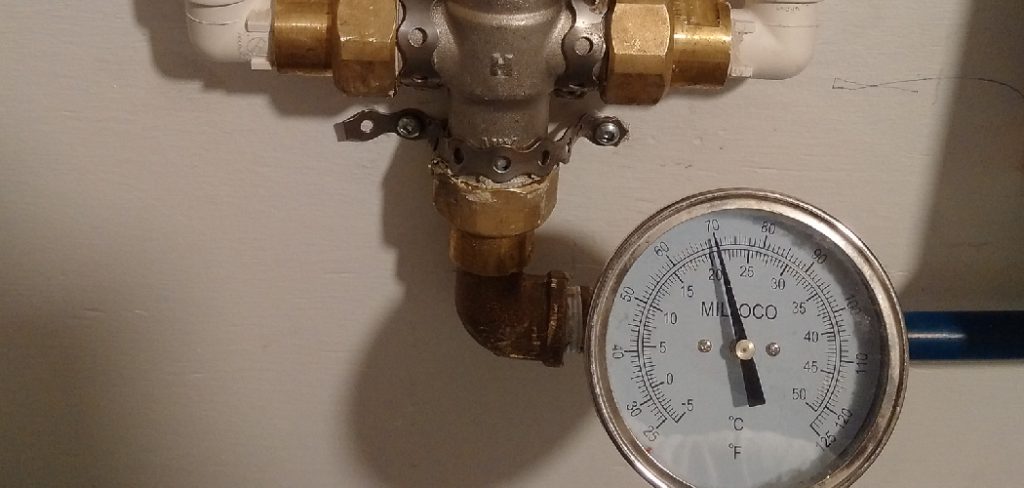
Hence, understanding “how to calibrate water pressure gauge” is vital to maintaining system efficiency and reliability. Calibration involves adjusting the gauge to ensure it provides precise measurements by comparing it with a standard reference. This process not only enhances the gauge’s accuracy but also extends its lifespan, ensuring optimal functionality for the systems it supports. By familiarizing themselves with the calibration process, operators can ensure consistent performance and prevent costly repairs or replacements.
Understanding Water Pressure Gauges and the Need for Calibration
How Water Pressure Gauges Work
Water pressure gauges are essential tools used to measure the force of water flowing through a system. They operate by employing either a Bourdon tube or an electronic sensor to detect changes in pressure. The Bourdon tube, a coiled hollow tube, flexes under pressure, causing a mechanical movement that translates into a needle reading on the gauge.
On the other hand, electronic sensors employ piezoelectric components to convert pressure changes into electrical signals, resulting in digital displays. Typically, these gauges display readings in units such as PSI (pounds per square inch), bar, or kilopascal (kPa), enabling standardized measurement across various applications.
Why Calibration Is Necessary
The calibration of water pressure gauges is critical to maintain their accuracy and reliability. Over time, gauges can drift from their original settings due to mechanical wear, exposure to environmental elements, or gradual stress from regular operation. Without regular calibration, these deviations can lead to misleading pressure readings, undermining system performance and potentially causing damage.
By routinely calibrating the gauges, operators ensure that measurements remain precise, which is essential for efficient and safe system functioning. Calibration not only corrects any drift but also helps identify underlying issues early, offering timely maintenance and avoiding costly repairs.
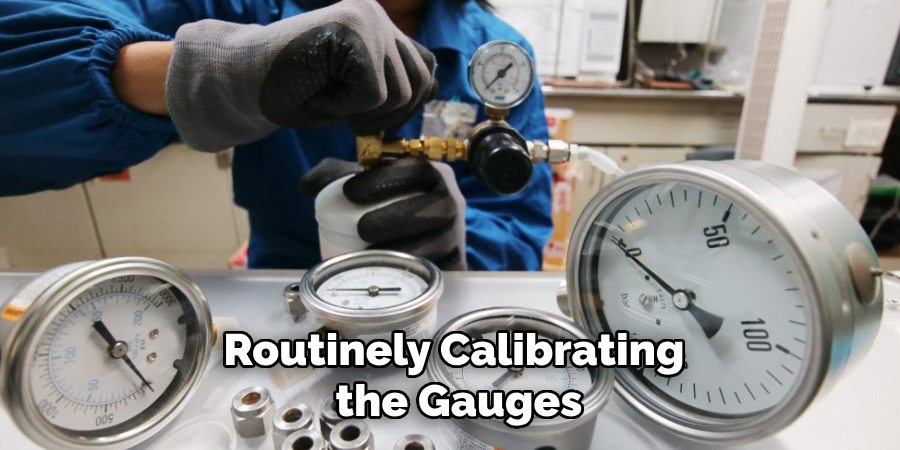
Tools and Materials Needed for Calibration
List of Required Tools
Several essential tools and materials are required to effectively calibrate a water pressure gauge. Firstly, having the right calibration equipment is crucial — either a certified reference gauge or a test bench is needed to ensure accuracy. Additionally, a set of wrenches is necessary to secure connections properly, alongside Teflon tape to seal any threaded joints and prevent leaks.
Adapters might be required to connect the gauge to various calibration devices or manifold setups. It’s also important to have cleaning supplies, such as brushes and cloth, to remove any debris or buildup on the gauge, ensuring precise readings.
Importance of Using Certified Reference Gauges
Certified reference gauges are vital as they provide a standard baseline for accuracy during calibration. These gauges undergo rigorous testing and certification, ensuring they meet industry standards. By comparing the tested gauge against a certified reference, users can achieve reliable and standardized measurements essential for optimal system performance.
Preparing the Gauge for Calibration
Cleaning and Inspecting the Gauge
Before calibrating a water pressure gauge, conducting a thorough inspection and cleaning is essential to ensure accurate readings. Start by examining the gauge for any visible signs of damage or wear, including scratches on the face or bent needles that might affect its operation. Pay close attention to the connection ports, checking for dirt, debris, or corrosion buildup that can impede functionality.
Utilizing a damp cloth, gently wipe the gauge’s surface to remove any dust or grime. For more stubborn debris, compressed air can be used to clear out the ports and other hard-to-reach areas. Ensuring the gauge is clean and free from obstructions aids in maintaining its precision and prolongs its service life.
Removing the Gauge from Its System
To safely remove the gauge for calibration, follow a methodical process to prevent damage and ensure safety. Begin by shutting off the system to relieve any built-up pressure, as sudden releases can be hazardous. Once the pressure has been effectively vented, use an appropriate wrench to carefully detach the gauge from its position. Be cautious not to overtighten or force the wrench, which can damage the threads or connection points.
Maintain control over the gauge during removal to prevent accidental drops or impacts that could misalign the internal components. Proper handling during this step ensures the gauge remains intact and functional for the calibration process.
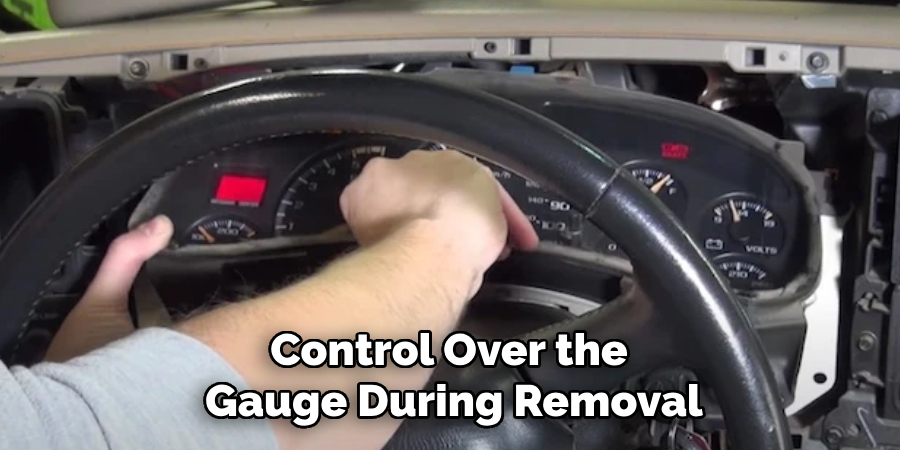
How to Calibrate Water Pressure Gauge: Calibration Methods
Using a Reference Gauge
To calibrate using a reference gauge, set up a test manifold that allows both the water pressure gauge and a certified reference gauge to connect simultaneously. Ensure the connections are secure to prevent leaks that could affect the readings. Begin by gradually applying pressure to the manifold. As the pressure increases, take readings from both gauges at various increments, typically every 10, 20, and 50 PSI.
Carefully document any differences observed between the two gauges. If discrepancies are found, adjustments may be necessary to bring the water pressure gauge in line with the reference standard. This method ensures the gauge’s output is consistent with industry standards, ultimately enhancing its reliability in practical applications.
Using a Deadweight Tester
A deadweight tester offers precise calibration by using known weights to apply a specific pressure. Attach the gauge to the deadweight tester’s port, ensuring a tight fit to prevent pressure loss. Begin the process by applying incremental weights, which exert standardized pressure on the gauge. As each weight is added, record the gauge’s reading and compare it to the expected standard.
Note any inconsistencies, as these indicate the need for calibration adjustments. The deadweight tester’s accuracy makes it reliable for confirming a gauge’s precision, particularly in critical applications where exact measurements are essential for safety and performance.
Adjusting the Water Pressure Gauge
Adjusting the water pressure gauge after identifying discrepancies during calibration is crucial to ensure accuracy. Begin adjustment by referencing the documented differences obtained during calibration. For analog gauges, carefully access the internal mechanism, typically located behind the face of the gauge. Use a small screwdriver or adjustment tool to tweak the calibration screw, minutely altering the spring tension or dial position to match the reference readings.
For digital gauges, adjustments may involve recalibrating the sensor electronics, which can require following specific manufacturer instructions. If possible, input the offset values directly into the gauge’s software to align the display with accurate measurements.
Identifying and Correcting Errors
Common calibration errors in water pressure gauges include over-reading, under-reading, and inconsistent readings. Over-reading occurs when the gauge shows a higher pressure than the actual, while under-reading reflects a lower pressure than the actual. Inconsistent readings can suggest internal mechanical issues or calibration drift.
Minor adjustments can often correct these errors by making precise tweaks to the gauge’s internal mechanism or recalibrating electronically for digital gauges, ensuring measurements align with standard values.
Recalibrating or Replacing the Gauge
Professional recalibration services should be considered for gauges that are unadjustable or display severe inaccuracies. Experts utilize advanced equipment to increase the gauge’s needed accuracy levels, prolonging its operational life. However, replacement may be the most viable solution if recalibration proves impractical or the gauge remains unreliable despite adjustments.
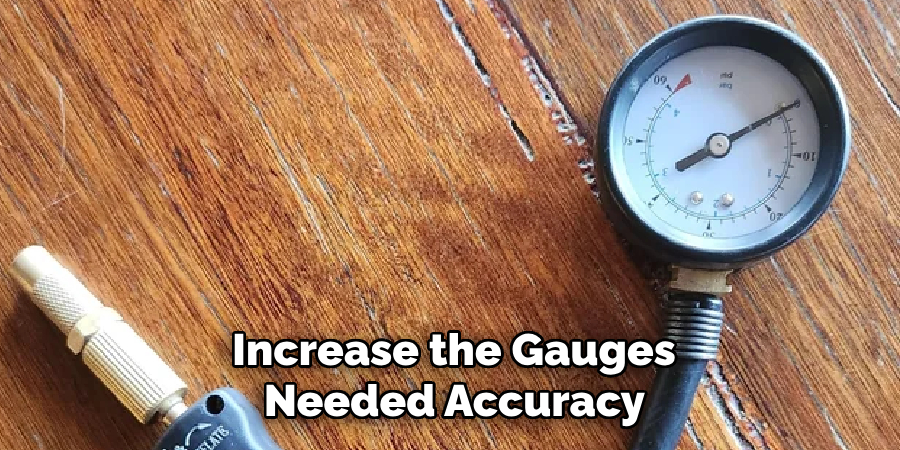
Investing in a new gauge ensures dependable readings, reducing the risk of system failure and maintaining optimal functionality.
Testing and Verifying Calibration Accuracy
Retesting After Calibration
After making any necessary adjustments to the water pressure gauge, it is crucial to retest to verify the effectiveness of the calibration. Reconnect the gauge to the system or test manifold with a reference gauge or calibrated instrument. Carefully repeat the initial test steps, gradually applying pressure and documenting the gauge’s readings at various increments as previously done during calibration.
Compare the results to the reference standard, ensuring that the gauge now reflects accurate measurements. If the gauge’s readings align closely with the reference, the calibration process has successfully demonstrated the gauge’s reliability and precision in practical applications.
Documenting Calibration Results
Accurate documentation of the calibration process is vital for ongoing maintenance and validation. Record all test data, including the initial readings, calibration adjustments made, and final post-calibration measurements. Additionally, note the calibration date and any environmental conditions that could impact readings, such as temperature or humidity.
This documentation ensures traceability and supports regular validation of the gauge’s accuracy over time. Establishing regular calibration intervals tailored to the gauge’s specific usage and application context maintains optimal performance and reduces the risk of erroneous pressure readings, thus supporting overall system safety and effectiveness.
Preventive Maintenance Tips for Water Pressure Gauges
Protecting Gauges from Damage
To protect water pressure gauges from damage, avoiding exposure to extreme pressure spikes, moisture, or corrosive substances is vital. Such conditions can compromise the gauge’s functionality and life span. Protective covers or enclosures can significantly shield gauges in harsh environments, preventing direct contact with damaging elements and ensuring long-lasting accuracy and reliability.
Establishing a Regular Calibration Schedule
A regular calibration schedule is essential to maintain precision and performance. For residential systems, calibrations should be carried out annually. High-usage setups benefit from a biannual calibration schedule to ensure continued accuracy. Additionally, periodic inspections should be conducted to catch early signs of wear or drift, allowing for timely maintenance and prevention of potential failures or inaccurate readings.
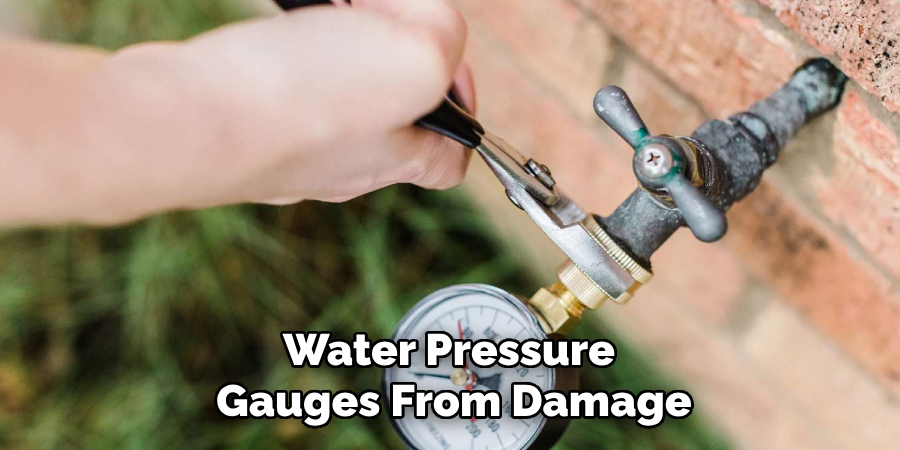
Conclusion
Accurate calibration of water pressure gauges is fundamental for ensuring optimal system performance and safety. Understanding “how to calibrate water pressure gauge” simplifies the task when equipped with the proper tools and steps. This straightforward process not only prevents system failure but also enhances reliability. Regular calibration should be prioritized, using the outlined practices to maintain accuracy and prevent potential issues.
Establishing a routine not only preserves the investment in equipment but also safeguards the entire system’s safety and operational integrity. By committing to these practices, users ensure dependable and precise water pressure measurements over time.