Understanding the pressure drop in a pipe is essential for designing efficient fluid flow systems. Pressure drop refers to the reduction in pressure as a fluid moves through a pipe due to factors like friction, changes in elevation, and flow
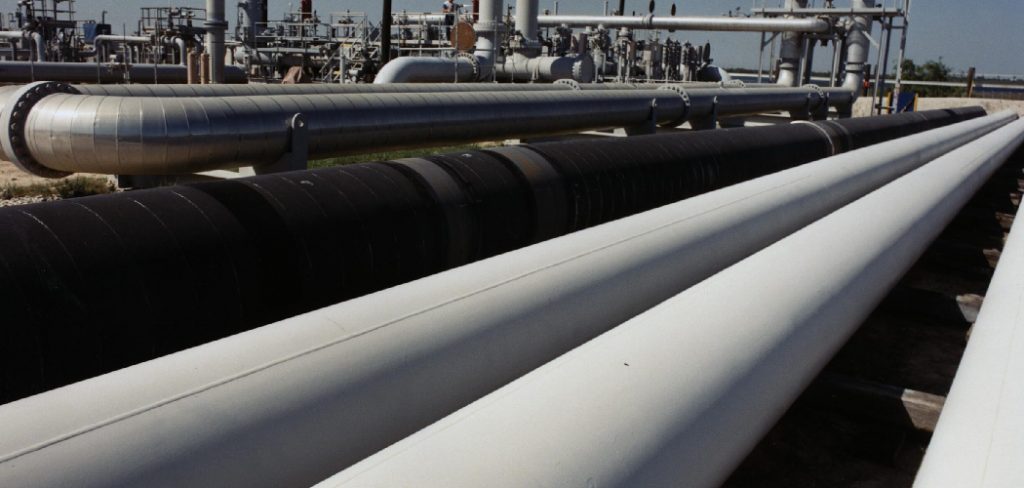
obstructions. Accurately calculating pressure drop helps ensure proper system performance, prevent energy losses, and maintain safety in various industrial and engineering applications. This guide provides an overview of how to find pressure drop in a pipe.
What is Pressure Drop?
Pressure drop is the decrease in pressure of a fluid as it flows through a piping system. This phenomenon occurs due to several factors, including friction between the fluid and the pipe walls, turbulence within the fluid, and obstructions or bends in the piping. Pressure drop is typically measured in units of pressure, such as pascals (Pa) or pounds per square inch (psi). It plays a critical role in fluid dynamics as it can affect the efficiency of the system, the flow rate of the fluid, and even the energy consumption of pumps or compressors. Understanding pressure drop is fundamental in designing systems that transport liquids or gases efficiently and safely.
Factors Affecting Pressure Drop
Several factors influence the pressure drop in a pipe, and understanding these can help in optimizing fluid flow systems. The key factors include:
- Pipe Diameter: Narrower pipes cause higher pressure drop due to increased frictional forces between the fluid and the pipe walls. Larger diameters reduce these forces, leading to a lower pressure drop.
- Fluid Velocity: The speed at which the fluid moves through the pipe directly impacts pressure drop. Higher velocities result in greater turbulence and friction, which increase the pressure drop.
- Fluid Viscosity: The viscosity of the fluid, or its resistance to flow, also affects pressure drop. Fluids with high viscosity, such as oil, experience more resistance and therefore a higher pressure drop compared to less viscous fluids like water.
- Pipe Length: The longer the pipe, the greater the surface area the fluid comes into contact with, which increases friction and results in a higher pressure drop.
- Roughness of Pipe Surface: The internal surface texture of the pipe can create additional resistance. Rough pipes or those with deposits and corrosion create more friction, leading to an increased pressure drop.
- Fittings and Valves: Elements such as bends, elbows, tees, valves, and other fittings disrupt the fluid flow and create additional resistance, adding to the overall pressure drop in the system.
- Changes in Elevation: If the pipe system involves changes in elevation, gravitational effects can either increase or decrease the pressure. Fluids flowing uphill will require more energy, resulting in a higher pressure drop.
By considering these factors during the design and operation of a piping system, engineers can minimize energy losses, improve efficiency, and ensure the system meets its performance requirements.
10 Easy Steps How to Find Pressure Drop in a Pipe
1. Using the Darcy-Weisbach Equation
The Darcy-Weisbach equation is one of the most versatile and accurate methods to calculate pressure drop. It is expressed as:
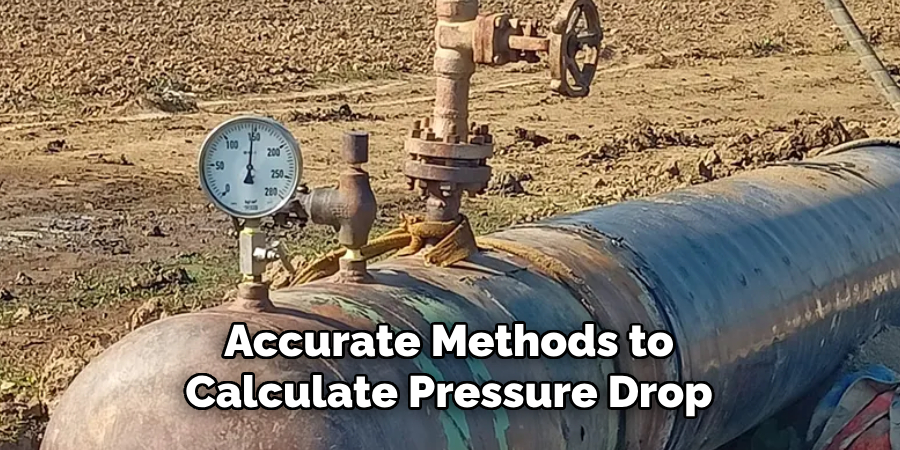
Where:
- : Pressure drop (Pa)
- : Friction factor (dimensionless)
- : Length of the pipe (m)
- : Internal diameter of the pipe (m)
- : Fluid density (kg/m³)
- : Flow velocity (m/s)
To use this equation effectively, calculate the Reynolds number to determine whether the flow is laminar or turbulent, as this will dictate the friction factor. The Darcy-Weisbach equation is ideal for incompressible fluids and is applicable across a variety of scenarios, making it indispensable in engineering design.
2. Using the Hazen-Williams Formula
For water flow in non-corrosive pipes, the Hazen-Williams formula provides a simpler alternative:
Where:
- : Pressure drop (psi)
- : Pipe length (ft)
- : Hazen-Williams coefficient (dimensionless)
- : Pipe diameter (inches)
- : Flow rate (gpm)
This equation is particularly useful for turbulent flow in water distribution systems. The coefficient varies with pipe material—higher values indicate smoother pipes. While less versatile than the Darcy-Weisbach equation, the Hazen-Williams formula is efficient for water systems.
3. Utilizing Online Pressure Drop Calculators
Online calculators simplify pressure drop calculations by requiring users to input basic parameters such as pipe diameter, length, fluid type, and flow rate. These tools are pre-loaded with databases of material properties and friction factors, eliminating manual calculations. While convenient and time-saving, users must ensure the accuracy of their inputs and select a reputable tool for reliable results.
4. Employing the Moody Diagram
The Moody diagram graphically represents the friction factor based on Reynolds number and relative pipe roughness. To use this method:
- Calculate the Reynolds number to determine the flow regime.
- Determine the relative roughness by dividing the pipe roughness by its diameter.
- Locate the friction factor on the diagram.
The friction factor obtained from the Moody diagram can then be used in the Darcy-Weisbach equation to compute pressure drop. This method is especially valuable for visual learners and provides a clear understanding of flow characteristics.
5. Using Computational Fluid Dynamics (CFD)
CFD software offers a powerful, high-precision approach to analyze fluid flow and pressure drops in complex systems. Programs like ANSYS Fluent or COMSOL Multiphysics simulate detailed flow behavior, including turbulence and
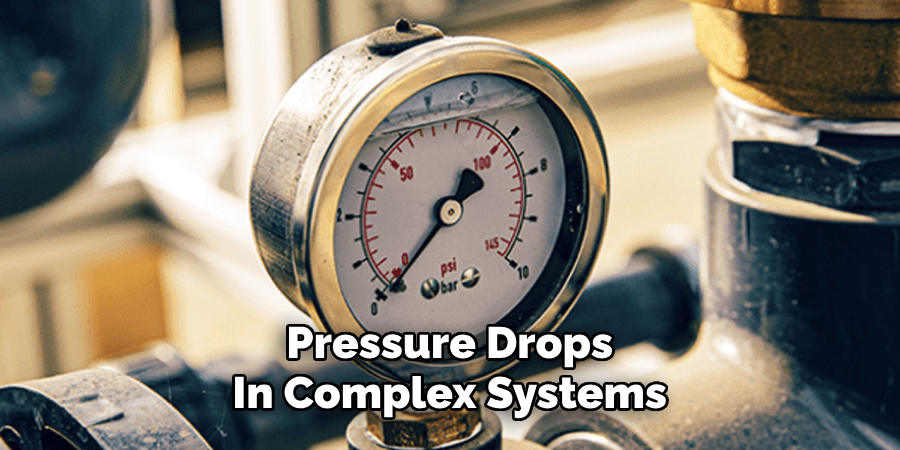
temperature effects. By creating a digital model of the pipe system, you can identify localized pressure drops and optimize designs. While highly accurate, this method requires advanced expertise and access to specialized software.
6. Measuring Directly with Pressure Gauges
A straightforward and practical approach is to measure pressure drop directly in an operational system. Install pressure gauges at the inlet and outlet of a pipe section to obtain the pressure difference. This method is particularly useful for troubleshooting or verifying theoretical calculations. Regular maintenance of the gauges ensures accurate readings, making this a reliable option for on-site measurements.
7. Applying the Bernoulli Equation
The Bernoulli equation provides a comprehensive energy balance in fluid systems. By accounting for kinetic energy, pressure, and potential energy, the equation is expressed as:
Where:
- , : Pressures at two points (Pa)
- : Frictional pressure drop (Pa)
- , : Heights (m)
- : Gravitational acceleration (m/s²)
By rearranging the equation to isolate , you can calculate pressure drop in systems with varying heights and velocities. This method is ideal for analyzing complex networks.
8. Accounting for Minor Losses
Fittings, valves, and bends introduce additional pressure losses, known as minor losses. These can be calculated using:
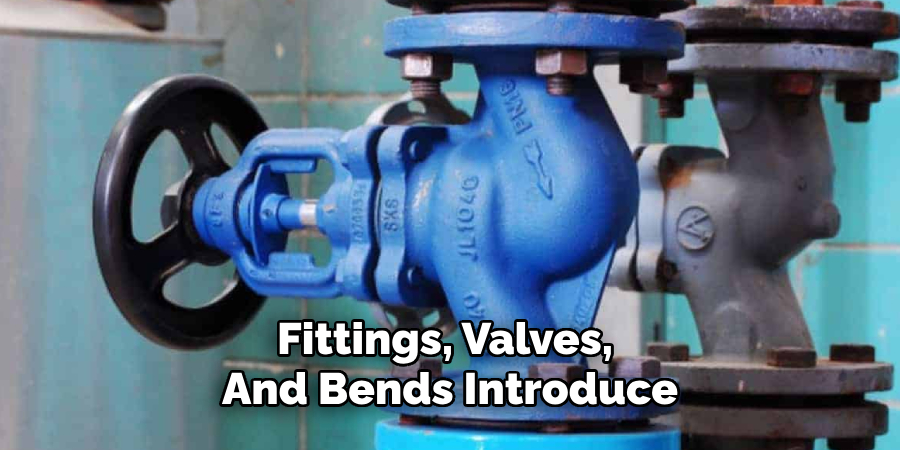
Where:
- : Loss coefficient (dimensionless)
Minor losses should be added to the frictional pressure drop for a complete assessment. Loss coefficients are typically provided by manufacturers or engineering standards. Ignoring these losses can lead to inaccurate calculations, especially in systems with numerous fittings.
9. Using Energy Balance Principles
An energy balance approach evaluates the total energy in a system, considering work done by pumps, frictional losses, and changes in kinetic and potential energy. This holistic method integrates multiple equations to provide a detailed understanding of pressure drop, making it suitable for large or complex fluid networks.
10. Simplifying with Empirical Formulas
In specific industries or for particular materials, empirical formulas derived from experimental data can offer quick pressure drop estimations. These formulas are tailored to common conditions and pipe types, streamlining calculations. While not as versatile as theoretical methods, they provide practical approximations for standard applications. Ensure the chosen formula aligns with your system parameters.
Things to Consider When Calculating Pressure Drop
When calculating pressure drop in fluid systems, several critical factors must be taken into account to ensure accuracy and reliability:
Type of Fluid
The physical properties of the fluid, such as viscosity, density, and compressibility, play a crucial role in determining pressure drop. Always use the correct fluid data to avoid errors.
Flow Regime
Understanding whether the flow is laminar or turbulent is essential, as it dictates which equations and friction factors to apply. The Reynolds number is a key indicator of the flow regime.
Pipe Material and Roughness
The material and internal surface condition of the pipe affect the friction factor and, subsequently, the pressure drop. For accurate results, include the pipe’s relative roughness in calculations.
System Geometry
The layout of the system, including pipe length, diameter, and fittings, influences pressure drop. Complex geometries with multiple bends or fittings can significantly increase resistance.
Minor Losses
Valves, elbows, tees, and other fittings contribute additional pressure losses. Neglecting these can lead to underestimations in total pressure drop.
Temperature Effects
Temperature changes can alter fluid viscosity and density, impacting calculations. Ensure the temperature-dependent properties are included for precise outcomes.
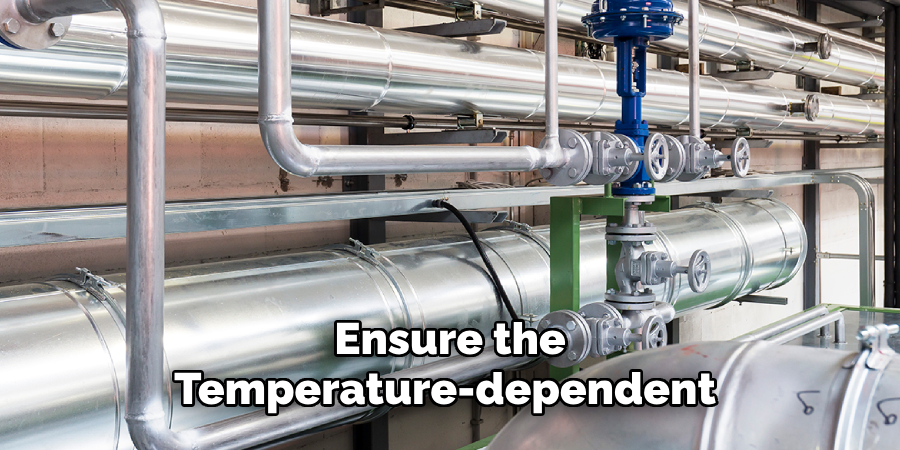
Accuracy of Input Data
Reliable calculations depend on accurate input parameters. Double-check pipe dimensions, fluid properties, and flow rates before conducting calculations.
Selected Method or Tool
Choose the appropriate method or formula based on system complexity and precision requirements. For large systems, advanced methods like CFD might be necessary, while simpler systems may only require an empirical formula.
By considering these factors, you can enhance the accuracy of your pressure drop analysis and optimize the performance of fluid systems.
Conclusion
Understanding and accurately calculating pressure drop is a fundamental aspect of designing and maintaining efficient fluid systems. By employing the right methods—ranging from theoretical formulas to advanced computational tools—you can identify potential inefficiencies and optimize system performance. Taking into account factors such as fluid properties, flow regime, system geometry, and minor losses ensures precise calculations and reliable results. Thanks for reading, and we hope this has given you some inspiration on how to find pressure drop in a pipe!