Insulating a vent pipe adapter is essential for maintaining an efficient and durable system. Insulation helps prevent heat loss, reduce energy consumption, and improve overall efficiency, especially in HVAC systems.
Additionally, it minimizes condensation buildup, which can lead to rust, corrosion, and eventual damage to the adapter and surrounding components. By ensuring the adapter is well-insulated, you can extend the lifespan of the pipes and reduce the risk of costly repairs.
Common applications for insulating vent pipe adapters include HVAC systems, furnace vent pipes, and exhaust ducts. Each system relies on insulation to regulate temperature and prevent unnecessary wear and tear.
The insulation process involves several key steps, including selecting the appropriate insulating material, preparing the adapter for installation, securely attaching the insulation, and sealing any remaining gaps. Understanding how to insulate adapter on vent pipes is a practical skill that ensures your system operates optimally and efficiently.
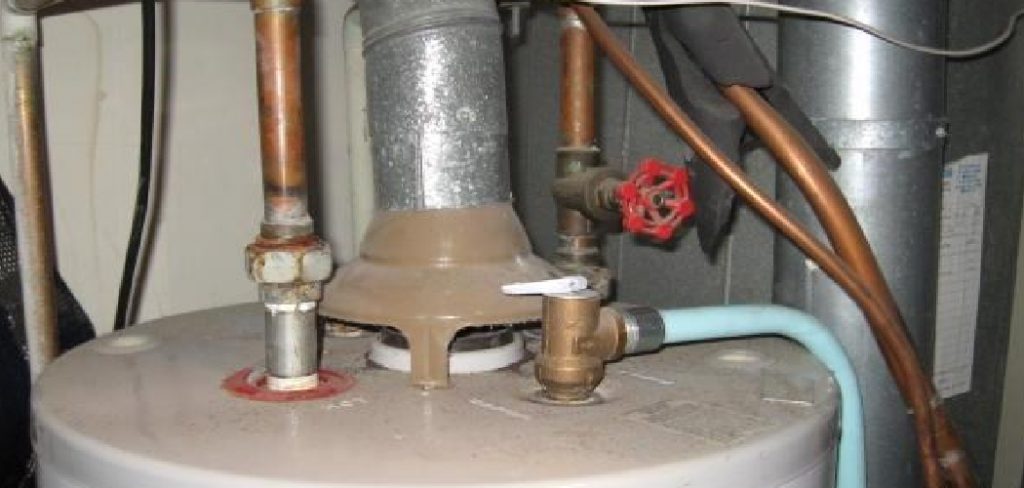
Choosing the Right Insulation Material
Types of Insulation for Vent Pipes
When insulating vent pipe adapters, selecting the appropriate insulation material is crucial to achieving optimal performance and durability. Several types of insulation cater to various needs:
- Fiberglass Pipe Wrap: Known for its high-temperature resistance, fiberglass pipe wrap is ideal for vent pipes exposed to extreme heat, such as those in industrial or specialized environments. This material effectively minimizes heat loss and prevents overheating.
- Foam Pipe Insulation: Lightweight and easy to install, foam pipe insulation is popular for residential HVAC applications. It provides reliable insulation for moderate temperature ranges and helps reduce condensation buildup.
- Reflective Foil Insulation: Designed to combat radiant heat, reflective foil insulation is best suited for applications requiring heat reflection, such as vent pipes near energy-intensive systems.
Factors to Consider
Selecting the right insulation material involves evaluating several factors to match the specific system requirements:
- Pipe Material: Some insulation types work better with metal pipes, while others are suitable for plastic or PVC pipes.
- Temperature Tolerance: The insulation must withstand the operating temperature of your system to ensure safety and efficiency.
- Indoor vs. Outdoor Use: Outdoor applications require weather-resistant insulation to protect against moisture, UV rays, and temperature fluctuations.
Careful consideration of these factors ensures the proper insulation material is chosen, enhancing the system’s reliability.
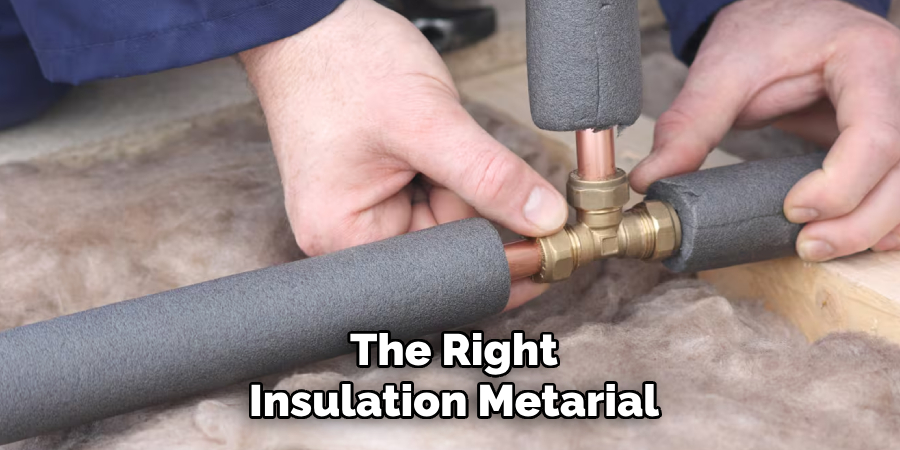
Preparing the Vent Pipe Adapter
Cleaning the Surface
Before attaching insulation to the vent pipe adapter, it is crucial to clean the surface thoroughly. Use a dry cloth or a mild cleaning solution to remove any dust, grease, or debris that may prevent proper adhesion. A clean surface ensures that the insulation or adhesive materials firmly attach without compromising performance.
Checking for Leaks or Gaps
Inspect the vent pipe adapter and its connections for any visible leaks or gaps. These can compromise the system’s efficiency and lead to heat loss or unwanted air exchange. Seal any openings with high-temperature silicone sealant or HVAC-grade tape, ensuring a secure and durable bond. Proper sealing enhances the insulation’s effectiveness and prolongs the system’s lifespan.
Measuring the Adapter and Pipe Sections
Accurate measurements are essential for the insulation material’s complete and snug fit. Measure the vent pipe adapter and adjacent pipe sections carefully, ensuring that all exposed areas are adequately covered.
Use a flexible measuring tape to account for any bends or irregularities in the pipe. Preparing insulation to fit these dimensions precisely will prevent gaps and ensure optimal thermal protection.
How to Insulate Adapter on Vent Pipes: Installing the Insulation
Proper insulation installation is crucial to maintaining efficiency and preventing heat loss. Follow these steps to ensure a thorough and effective process when insulating the vent pipe adapter:
Wrapping Fiberglass or Foam Insulation Around the Adapter
Select appropriate insulation materials, such as fiberglass or foam, that can withstand high temperatures and provide sufficient thermal resistance. Carefully wrap the chosen insulation material around the vent pipe adapter, ensuring complete coverage. Always align the insulation evenly, avoiding any gaps or unprotected areas. This step ensures proper thermal regulation and prevents unnecessary energy waste.
Cutting to Fit Snugly Around the Vent Connection
Cut the insulation to fit snugly around the vent connection using a utility knife or a pair of sharp scissors. Accurately trimming the material ensures that it conforms precisely to the shape and dimensions of the pipe and adapter. This step is crucial when dealing with irregular sections or bends, as it reduces the likelihood of leaving exposed surfaces. Double-check the cuts to guarantee a secure fit before proceeding to secure the insulation.
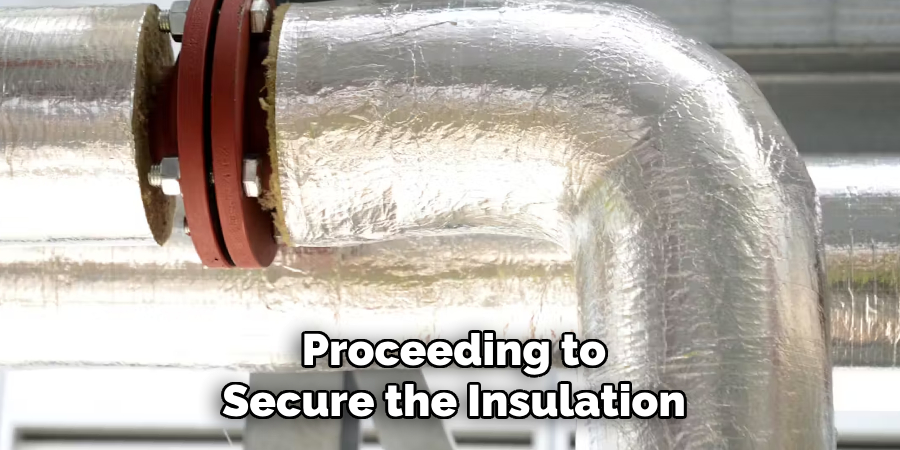
Using Tape or Clamps to Secure the Insulation
Once the insulation is correctly positioned, use high-temperature tape or metal clamps to secure it in place. Wrap the tape tightly around the insulation or fasten the clamps firmly regularly, ensuring the material remains stable and does not shift over time.
Be careful not to compress the insulation excessively, as this could compromise its thermal performance. The goal is to maintain the material’s structure while creating a secure bond that keeps the insulation in position long-term.
Overlapping Sections for Maximum Coverage
For optimal thermal protection, make sure to overlap the insulation sections slightly when wrapping them around the adapter and pipe. Overlapping eliminates gaps that could lead to heat loss or unwanted air leakage, enhancing the system’s overall efficiency.
Inspect each section during the process to confirm complete coverage, and apply additional tape or sealant if necessary to seal any small openings. Properly installed and overlapped insulation significantly improves energy efficiency and contributes to the durability of the venting system.
Sealing and Weatherproofing the Insulation
Proper sealing and weatherproofing are essential for ensuring the durability and long-term efficiency of the insulated venting system. This step involves securing seams, filling gaps, and protecting against environmental factors like moisture or extreme temperatures.
Applying Foil Tape or High-Temperature Duct Tape
To secure the insulation’s seams, use foil or high-temperature duct tape. These materials are designed to withstand the heat generated by the venting system while maintaining a strong bond over time. Carefully apply the tape along each seam, pressing firmly to ensure a tight seal.
Avoid leaving any gaps, as exposed seams can lead to heat loss and reduce the system’s overall effectiveness. To maintain a clean and professional finish, smooth out any wrinkles or bubbles during application. This step secures the insulation in place, prevents air leakage, and ensures the system remains efficient and reliable under regular operation.
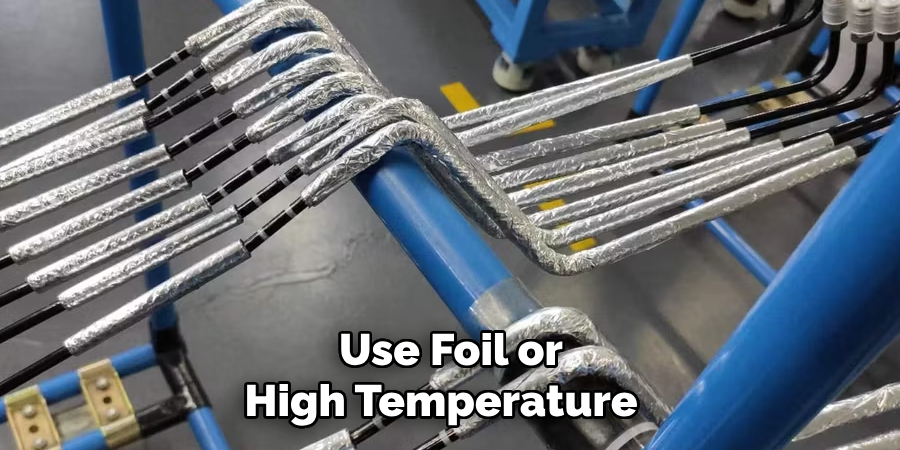
Using Spray Foam for Hard-to-Reach Areas
Applying spray foam insulation is an effective solution for small gaps or hard-to-reach areas around the adapter and pipe. Spray foam expands to fill even the tiniest crevices, creating an airtight seal that enhances thermal efficiency.
Gently apply the foam to areas where traditional insulation materials, such as tight corners or joint connections, cannot provide adequate coverage. Allow time for the foam to cure and harden according to the product instructions.
Once fully set, trim any excess foam to prevent obstruction or interference with the venting system’s operation. This step is particularly useful for ensuring a complete barrier against heat loss and airflow without compromising accessibility.
Waterproofing for Outdoor Installations
Outdoor installations are especially susceptible to moisture, so adding a waterproof layer is essential to protect the insulation. Wrap the insulated sections with a protective waterproof jacket or wrap, ensuring it is securely fastened with tape or clamps.
This additional layer prevents water infiltration, which could compromise the insulation’s performance or lead to structural damage over time. Selecting weather-resistant materials designed for outdoor use ensures longevity even in harsh environments.
Regular inspections and maintenance are recommended to verify that the waterproof barrier remains intact and effective.
By thoroughly sealing and weatherproofing the insulation, your venting system will maintain optimal efficiency and resist environmental wear, ultimately prolonging its lifespan and reducing energy costs.
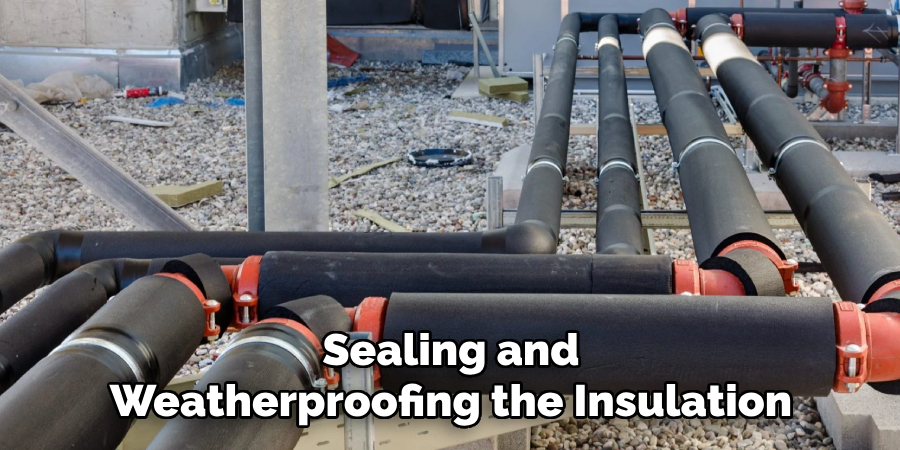
Testing and Inspecting the Insulated Adapter
Checking for Proper Fit and Coverage
After installing and weatherproofing the insulated adapter, testing and inspecting the system to ensure optimal performance is crucial.
Begin by examining the insulated sections for proper fit and full coverage, verifying that the insulation is securely fastened and free from gaps or loose areas. Any exposed sections could lead to inefficiencies or environmental damage and should be addressed immediately.
Monitoring for Condensation or Heat Loss
During operation, check for any signs of condensation or heat loss around the adapter. Persistent condensation might indicate inadequate waterproofing or gaps in the insulation. Use a thermal imaging camera or a temperature probe to detect heat loss and identify areas requiring adjustment.
Correct any issues promptly by reinforcing and resealing insulation as necessary. Routine testing and inspection ensure the insulated adapter remains efficient and durable, maintaining its intended purpose for the long term.
Common Mistakes to Avoid
Using the Wrong Insulation Material
One of the most frequent mistakes is selecting an insulation material that is not suitable for the specific application. Some insulation types cannot withstand high temperatures and may melt or degrade over time, leading to system inefficiencies and potential hazards. Always choose insulation materials that are rated for the operating conditions of your system.
Not Sealing the Insulation Properly
Improper sealing of insulation is another common issue. Loose or uneven insulation can leave gaps that allow significant heat loss and condensation buildup, compromising the system’s performance and durability. Ensure all sections of insulation are securely fastened and sealed to prevent such problems.
Blocking Ventilation Clearance
Adequate airflow is essential for both performance and safety. Restricting ventilation by blocking clearance areas can result in overheating, inefficiencies, or even hazardous conditions. Always maintain proper ventilation clearance as specified by the system guidelines.
Conclusion
Proper insulation is crucial for the efficiency and safety of your system. Key steps include carefully choosing the right insulation for the application, wrapping and securing it properly, and sealing any gaps to avoid heat loss or moisture buildup.
Proper installation prevents inefficiencies, moisture damage, and potential hazards, ensuring long-term performance. For best results, use high-quality materials and periodically check for wear or damage in the insulation.
If you’re unsure how to insulate adapter on vent pipes, consult professional guidelines to guarantee a secure and effective installation. Following these practices will maximize your system’s durability and performance.