Measuring G.I. (Galvanized Iron) fittings is an essential process to ensure proper fit and compatibility in piping systems.
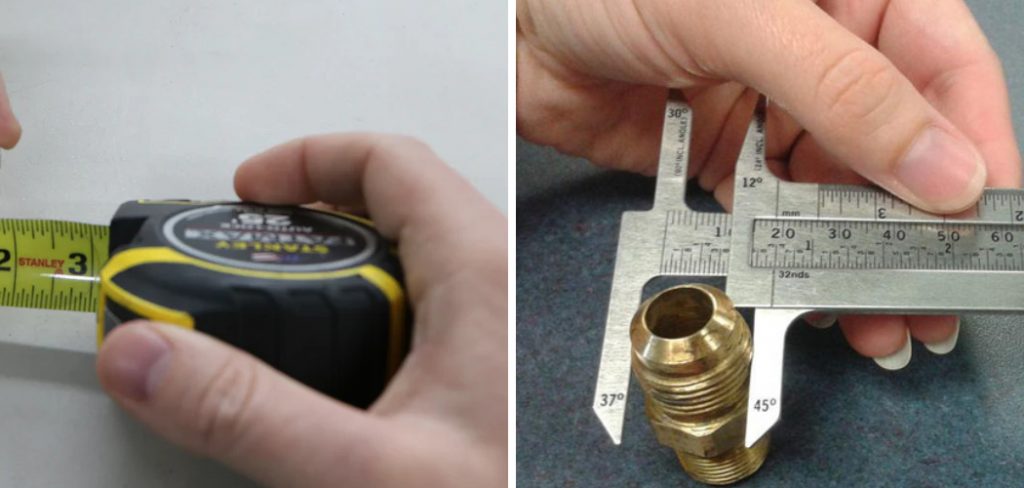
Accurately gauging the dimensions of these fittings helps maintain the integrity, safety, and efficiency of the installation. This guide provides an overview of the tools and methods required for how to measure G.I. fittings, ensuring reliable results for both residential and industrial applications.
What Are G.I. Fittings?
G.I. fittings, or Galvanized Iron fittings, are components used in piping systems to connect, change directions, or regulate the flow of water, gas, or other substances. These fittings are made from iron coated with a layer of zinc, which protects them from rust and corrosion, ensuring long-term durability even in harsh environments. Common types of G.I. fittings include elbows, tees, couplings, reducers, and unions. They are widely used in plumbing, construction, and industrial applications due to their strength, affordability, and resistance to wear and tear. Selecting the proper G.I. fitting is crucial for creating a secure and efficient system.
Importance of Accurate Measurement
Accurate measurement of G.I. fittings is vital to ensure the proper functioning and efficiency of any piping system. Incorrectly measured fittings can lead to misalignments, leaks, and structural instability, potentially resulting in costly repairs and reduced system performance. Furthermore, precise measurements help to avoid wastage of resources by ensuring that fittings match seamlessly with pipes and other system components. This is especially critical in environments where high-pressure flows or hazardous substances are involved, as even minor errors in fitting dimensions can pose significant safety risks. By taking the time to measure fittings correctly, professionals can ensure a reliable, durable, and efficient system installation.
Tools Needed for Measuring G.I. Fittings
To accurately measure G.I. fittings, having the right tools is essential. These tools help ensure precise dimensions, making installation smoother and more efficient. Below is a list of commonly used tools for measuring G.I. fittings:
- Measuring Tape: A flexible and straightforward tool for measuring the external dimensions of fittings such as length, diameter, and circumference.
- Vernier Caliper: Ideal for measuring internal and external diameters with high precision, a vernier caliper is indispensable for smaller or more refined measurements.
- Thread Gauge: A tool specifically designed to measure the pitch and diameter of threads in threaded fittings, ensuring compatibility with corresponding pipe threads.
- Ruler or Straight Edge: Useful for measuring flat sections or verifying straight edges on fittings.
- Pipe Diameter Tape (Pi Tape): Designed for quickly measuring the outside diameter of cylindrical objects, which is particularly helpful with round fittings.
- Marker or Chalk: Can be used to mark specific points or reference measurements on fittings during the process.
- Notebook or Documentation Tool: Essential for recording measurements accurately for future reference or project requirements.

Having these tools readily available allows professionals to measure G.I. fittings efficiently and with confidence, ensuring a successful and precise installation.
10 Methods How to Measure G.I. Fittings
1. Determine the Nominal Size of the Fitting
The nominal size of a G.I. fitting refers to the internal diameter of the pipe it connects to. Use a caliper or a measuring tape to measure the inner diameter (ID) of the pipe or fitting. This measurement is critical because G.I. fittings are classified based on their nominal size. For threaded fittings, ensure you measure the internal diameter of the female threads or the external diameter of the male threads accurately.
2. Measure the Thread Size
Thread size plays a crucial role in determining the compatibility of G.I. fittings. Use a thread gauge to measure the pitch and size of the threads. Thread pitch is the distance between the crests of adjacent threads, typically measured in millimeters or threads per inch. Accurately identifying the thread size ensures that the fitting will securely connect to the corresponding pipe or fitting.
3. Identify the Fitting Type
G.I. fittings come in various types, including elbows, tees, reducers, couplings, and unions. Each type has unique dimensions that must be measured. For example, measure the angle of an elbow fitting (e.g., 90° or 45°) and the branch diameter of a tee fitting. Identifying the fitting type helps determine the specific measurements required for proper installation.
4. Measure the Outside Diameter (OD)
The outside diameter (OD) of a G.I. fitting is another critical dimension. Use a caliper or a flexible measuring tape to
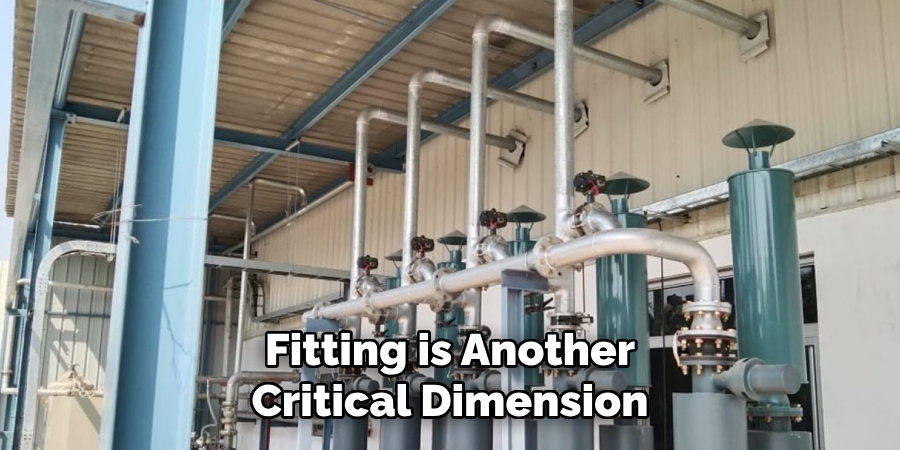
measure the OD of the fitting’s body and threads. Accurate OD measurements are essential for selecting the correct insulation, clamps, or supports for the fitting. Ensure the measuring tool is perpendicular to the fitting to avoid errors.
5. Account for Wall Thickness
The wall thickness of a G.I. fitting affects its durability and flow capacity. Use a micrometer or ultrasonic thickness gauge to measure the thickness of the fitting’s walls. Subtract the internal diameter from the outside diameter and divide by two to calculate the wall thickness. This measurement is especially important for high-pressure systems where thicker walls are required.
6. Measure the Overall Length
The overall length of a G.I. fitting is the distance from one end to the other, including any threaded sections. Use a measuring tape or ruler to measure the length accurately. For fittings with multiple branches, such as tees or crosses, measure each branch individually. Accurate length measurements ensure that the fitting will fit within the available space in the piping system.
7. Check for Center-to-End Dimensions
For fittings like elbows and tees, the center-to-end dimension is crucial. This measurement represents the distance from the centerline of the fitting to the end of the pipe connection. Use a caliper or measuring tape to measure this dimension for each branch of the fitting. Center-to-end dimensions are critical for ensuring proper alignment and spacing in piping systems.
8. Measure the Socket Depth
Socket depth refers to the distance a pipe can be inserted into a fitting. Use a depth gauge or ruler to measure the socket depth of a G.I. fitting. For threaded fittings, measure the depth of the female threads. Proper socket depth measurements ensure a secure and leak-free connection between the fitting and the pipe.
9. Account for Taper in Threaded Fittings
Threaded G.I. fittings often have tapered threads, which create a tight seal when connected. Use a thread gauge or a
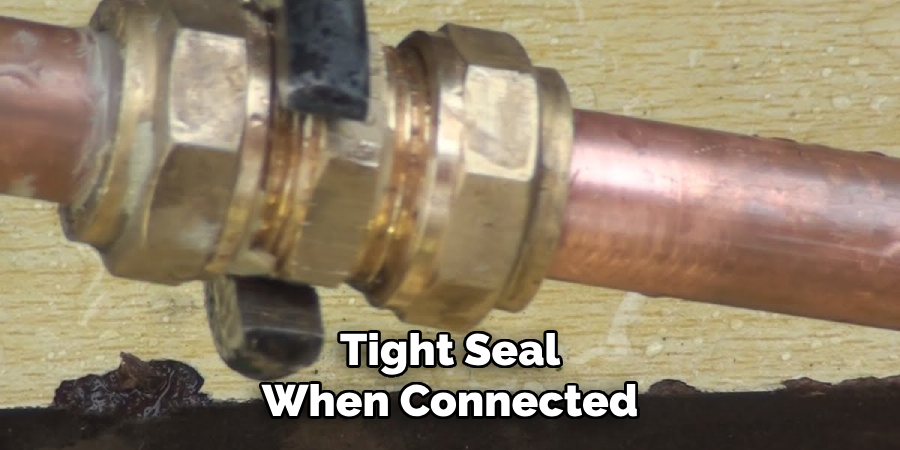
caliper to measure the taper angle and verify that it matches the corresponding pipe. Tapered threads are typically specified in standards such as BSP (British Standard Pipe) or NPT (National Pipe Thread). Accurate taper measurements ensure compatibility and prevent leaks.
10. Use Digital Measuring Tools for Precision
Digital measuring tools, such as digital calipers and laser distance meters, provide precise measurements for G.I. fittings. These tools are especially useful for complex or hard-to-reach fittings. Digital calipers can measure dimensions such as OD, ID, and thread size with high accuracy, while laser meters can measure the length and alignment of fittings in large systems. Using digital tools reduces measurement errors and improves efficiency.
Maintenance and Upkeep of G.I. Fittings
Regular maintenance and proper upkeep of G.I. fittings are essential for ensuring their longevity and consistent performance in piping systems. Here are some key practices to follow:
- Periodic Inspection: Regularly inspect G.I. fittings for signs of corrosion, wear, or damage. Focus on joints, threads, and areas exposed to moisture or harsh environments, as these are more prone to degradation.
- Cleaning: Remove dirt, debris, and buildup from the fittings using a soft brush and mild cleaning solution. Avoid using abrasive tools that can scratch or damage the fitting’s surface.
- Check for Leaks: Monitor the system for any leaks around the fittings. If leaks are detected, tighten the connections or replace the damaged fittings to prevent further issues.
- Lubricate Threads: Apply thread sealant or pipe joint compound to threaded fittings during installation or maintenance to ensure a secure, leak-proof connection. This also reduces the risk of thread corrosion over time.
- Protect Against Corrosion: Use protective coatings, painting, or galvanization to shield G.I. fittings from rust and corrosion, especially in outdoor or humid conditions. Regularly touch up these coatings as needed.
- Monitor Water Quality: Poor water quality can accelerate corrosion in G.I. fittings. Consider installing filters or water treatment systems to minimize harmful elements such as high acidity or dissolved salts.
- Replace Worn or Damaged Fittings: Promptly replace any fittings that show signs of significant wear, cracks, or deformation to maintain system integrity and avoid potential failures.
- Maintain Proper Pressure Levels: Ensure the piping system operates within the recommended pressure range for G.I. fittings, avoiding sudden pressure fluctuations or surges that may weaken connections.
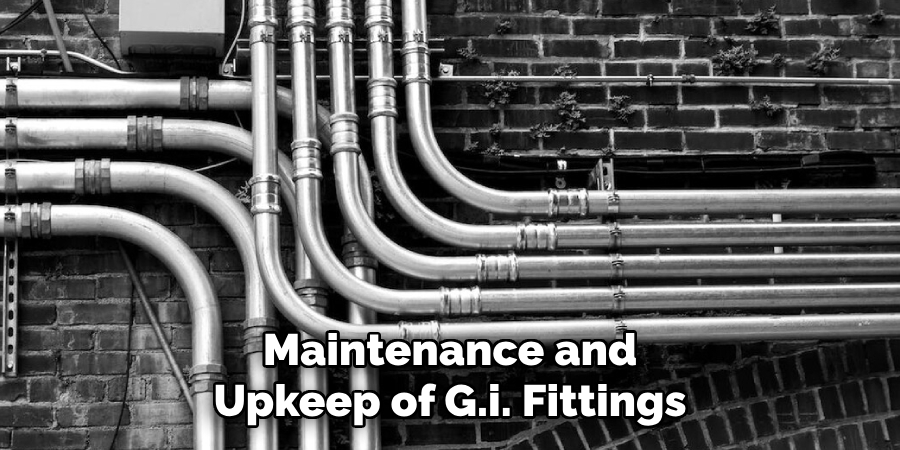
By dedicating time to maintenance and addressing issues proactively, you can extend the functional lifespan of G.I. fittings while maintaining a safe and efficient piping system.
Conclusion
G.I. fittings are a vital component of robust and reliable piping systems, and their performance heavily depends on accurate measurements, proper installation, and regular maintenance. By following the outlined measurement techniques, you can ensure precise fitting selection and compatibility, reducing the risk of leaks and system failures. Thanks for reading our blog post on how to measure G.I. fittings! We hope you found it helpful and informative.