Measuring pipe insulation is an essential step in ensuring proper energy efficiency and protecting pipes from extreme
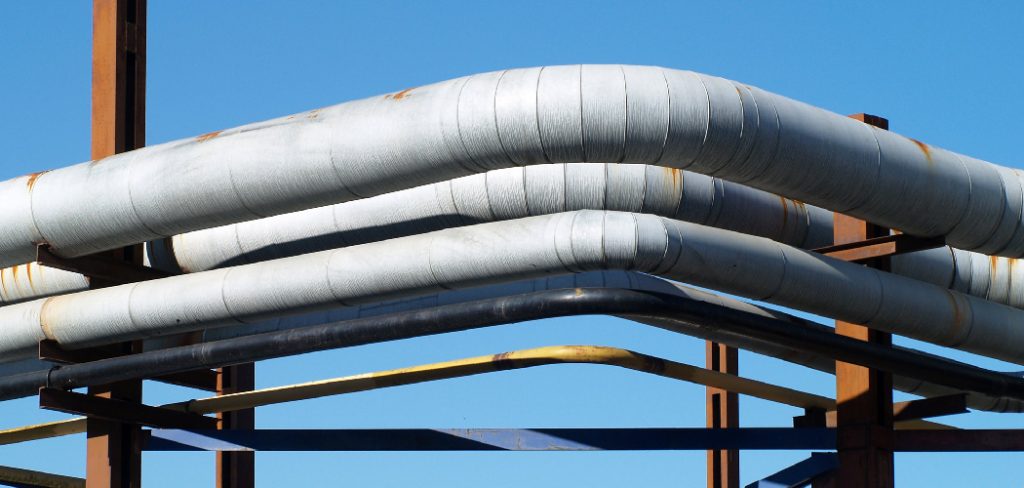
temperatures. Whether you’re working on a residential or commercial project, accurate measurements help determine the right amount and type of insulation needed for optimal performance. This guide will walk you through the process of how to measure pipe insulation effectively to achieve professional results.
Importance of Accurate Measurements
Accurate measurements are crucial when it comes to pipe insulation for several reasons. Properly measured insulation ensures complete coverage, reducing heat loss and preventing condensation, which can lead to corrosion or mold growth. Incorrect measurements may result in gaps or overlapping material, compromising the insulation’s effectiveness and leading to higher energy costs. Additionally, accurate measurements help avoid material wastage, saving both time and money during installation. By taking precise measurements, you can ensure that the insulation fits securely, providing long-term protection and energy efficiency.
Why Measuring Pipe Insulation Matters
Measuring pipe insulation matters because it directly impacts the performance and longevity of your insulation system. Incorrect measurements can lead to several issues, including inefficient energy use, increased utility costs, and potential damage to the piping system. For instance, insufficient insulation leaves pipes vulnerable to temperature extremes, which can cause freezing or overheating, resulting in costly repairs. On the other hand, excessive insulation thickness can be wasteful and may interfere with pipe functionality in tight spaces. Properly measured insulation not only ensures energy efficiency but also safeguards against environmental factors like moisture and fluctuating temperatures. Ultimately, accurate measurements are the foundation for a successful installation that delivers reliable protection and optimal performance over time.
Tools and Materials Needed
To measure pipe insulation accurately, you will need specific tools and materials to ensure precision and efficiency. Here’s a list of what you’ll need:
- Measuring Tape: A flexible measuring tape is essential for determining the length and circumference of the pipe. Ensure it is durable and marked clearly for accurate readings.
- Caliper or Pipe Diameter Tape: Use a caliper or specialized pipe diameter tape to measure the pipe’s exact diameter, which is critical for selecting the correct insulation size.
- Marker or Chalk: A marker or chalk will help you mark measurements directly on the pipe or insulation material for reference.
- Notepad and Pen: Having a notepad and pen allows you to record measurements systematically to avoid errors.
- Straightedge or Ruler: A straightedge may be required for cutting or marking insulation lengths accurately.
- Utility Knife or Insulation Cutter: These tools help trim insulation material to the required lengths with precision.
- Safety Gear: Safety glasses and gloves provide protection while cutting and handling insulation materials.
- Insulation Samples: Having various samples of insulation on hand can help select the appropriate type and thickness for the project.

Having these tools and materials ready ensures that the measuring process is seamless, precise, and efficient, leading to a professional insulation installation.
10 Methods How to Measure Pipe Insulation
1. Measure the Pipe Diameter
The first step in measuring pipe insulation is determining the pipe’s diameter. Use a pipe caliper or a flexible tape measure to measure the outside diameter (OD) of the pipe. Wrap the tape around the pipe, ensuring it is snug but not overly tight, and note the measurement. Knowing the OD is critical because insulation products are typically labeled based on the pipe diameter they are designed to fit. If you don’t have a caliper, you can use a string to measure the pipe’s circumference and divide it by π (3.1416) to calculate the diameter.
2. Determine the Wall Thickness
Pipe wall thickness influences the insulation thickness needed for adequate coverage. Consult the pipe specifications or use an ultrasonic thickness gauge to measure the wall. For standard pipes, referencing charts that correlate pipe diameter to wall thickness can also help. Accurately determining wall thickness ensures the insulation will accommodate both the inner flow diameter and the external pipe structure.
3. Account for Insulation Thickness Requirements
Once the pipe dimensions are established, determine the insulation thickness required based on the application and environment. Consider factors like temperature, energy loss prevention, and compliance with building codes or industry standards. Most insulation materials come in standard thicknesses such as ¼ inch, ½ inch, or 1 inch. For environments with extreme temperatures, thicker insulation may be necessary.
4. Measure Pipe Length
Accurate measurement of the pipe’s length is crucial to purchase the right amount of insulation. Use a flexible measuring tape and follow the contours of the pipe, especially for bends and elbows. For complex piping systems, measure each section individually and add the totals to ensure sufficient material. It’s advisable to account for an additional 5-10% to accommodate errors or adjustments during installation.
5. Consider Fittings and Valves
Pipes often include fittings, valves, and flanges, which require additional insulation. Measure the dimensions of these components separately, noting their diameter, length, and shape. Specialized pre-formed insulation pieces or flexible
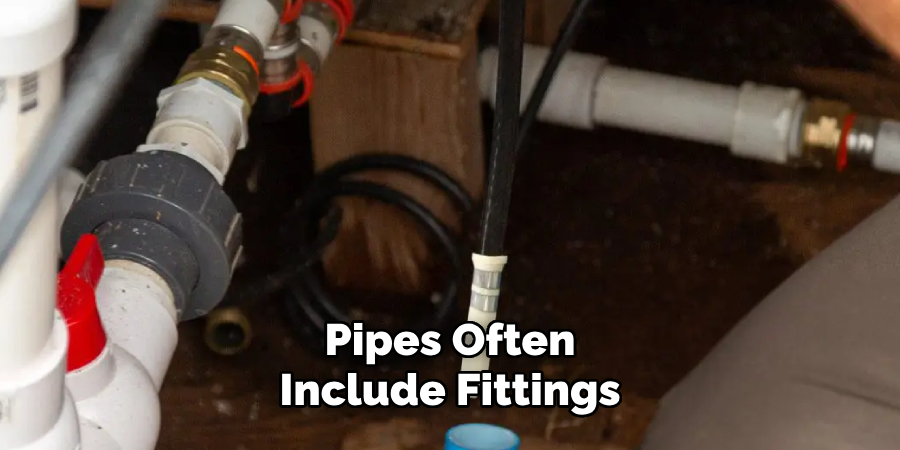
materials can be used to cover irregular shapes. Adding extra insulation material for these components ensures comprehensive coverage and prevents thermal bridging.
6. Measure for Outdoor Applications
If the pipe is exposed to outdoor conditions, measure its location and surroundings to account for additional protective layers. Outdoor insulation often requires a weatherproof jacket to shield it from UV rays, moisture, and physical damage. Include the dimensions of the protective jacket in your measurements and choose insulation materials that can withstand environmental stressors.
7. Check Clearance Around the Pipe
Before installing insulation, measure the clearance around the pipe to ensure there’s enough space for the chosen material. Use a ruler or measuring tape to determine the distance between the pipe and nearby walls, ceilings, or other pipes. If the clearance is tight, consider using low-profile insulation materials or adjusting the pipe layout to create additional space.
8. Measure Irregular Pipe Sections
For irregular sections, such as curved pipes, elbows, or junctions, use a flexible tape measure or tailor’s tape. Wrap the tape along the pipe’s contours to capture the full length and shape. Alternatively, use a flexible string to trace the section, then measure the string to determine the length. Specialized insulation wraps or custom-cut pieces can be used to cover these areas effectively.
9. Use Digital Tools and Software
Digital tools, such as laser distance meters or pipe measurement apps, can simplify the measurement process. Laser
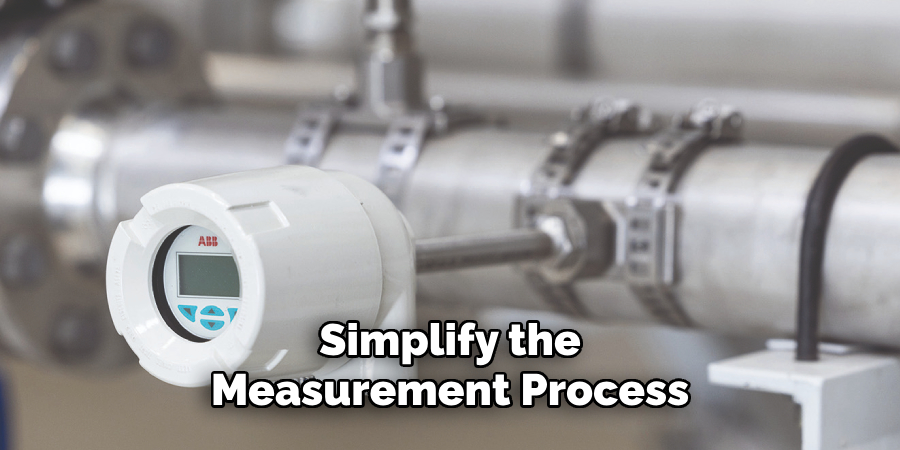
meters are particularly useful for hard-to-reach or complex piping systems, providing precise measurements from a distance. Many software programs allow you to input pipe dimensions and calculate the required insulation automatically, including allowances for bends, fittings, and environmental factors.
10. Consult Manufacturer Guidelines
Manufacturers of insulation materials often provide detailed guidelines and charts to help you measure and select the right product. These resources typically include information on recommended thicknesses, installation procedures, and compatibility with different pipe materials. Following these guidelines ensures that your measurements align with the manufacturer’s specifications, resulting in optimal performance and compliance with industry standards.
Troubleshooting Common Issues
Even with precise measurements and high-quality materials, issues can arise during the pipe insulation process. Below are common problems and how to address them:
1. Misaligned or Loose Insulation
Insulation that appears misaligned or slips out of place can lead to thermal bridging and energy loss. To fix this, ensure that the insulation is cut to the correct length and fits snugly around the pipe. Use proper adhesives, securing bands, or insulation-specific tapes to keep it firmly in place. Recheck measurements if the problem persists.
2. Gaps at Fittings and Joints
Fittings, valves, and junctions often leave gaps if not properly insulated. Use pre-formed insulation pieces or flexible materials designed for irregular shapes. Ensure the pieces are cut precisely and overlap slightly to eliminate gaps. Sealing with insulation tape or mastic can further prevent air or heat leakage.
3. Insufficient Clearance
If the space around the pipe is too tight for the selected insulation, it can lead to installation difficulties or inadequate coverage. Consider using low-profile or thin but high-performance insulation types. If possible, adjust nearby structures or reroute the pipe to create more space.
4. Damage to Insulation Surface
During installation or over time, the insulation’s outer surface may become torn or punctured, compromising its effectiveness. Repair the damage with compatible patching materials or replace the affected section entirely. For outdoor pipes, consider adding a protective jacket to shield against physical impact and environmental wear.
5. Condensation on Pipe Surface
Insufficient or incorrectly installed insulation can allow condensation to form on pipes, especially in humid environments.
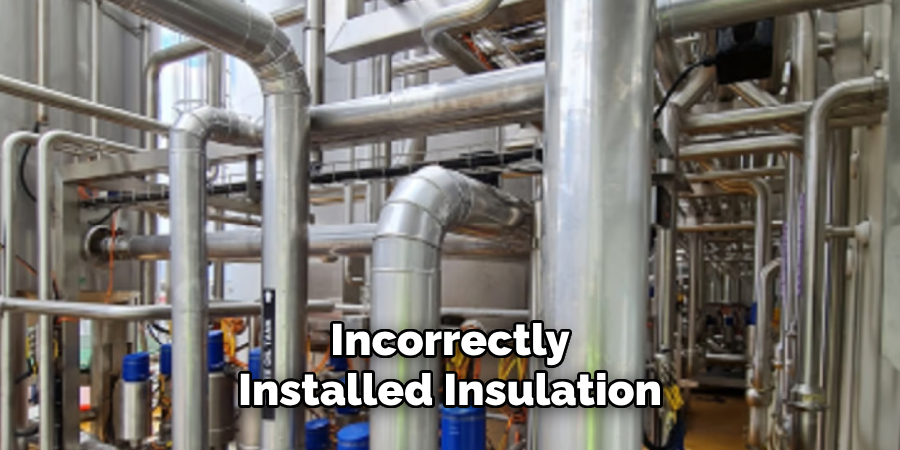
Verify that the insulation matches the requirements for temperature and moisture control. Seal all joints, edges, and seams properly to prevent moisture infiltration.
6. Difficulty in Insulating Complex Piping
Complicated piping systems with numerous bends and junctions can create challenges for insulation coverage. Use flexible insulation materials or custom-cut sections for these areas. Digital tools or templates can assist in creating accurate cuts for a better fit.
Conclusion
Measuring pipe insulation accurately is a multi-step process that involves determining pipe dimensions, insulation thickness, and system requirements. By following these methods, you can ensure proper insulation coverage, improve energy efficiency, and extend the lifespan of your piping system. So, there you have it – a quick and easy guide on how to measure pipe insulation.