Press fitting systems are an innovative and reliable solution for connecting pipes in plumbing, heating, and gas installations. They utilize a simple press tool to create secure, leak-proof connections without the need for soldering, threading, or welding. This method not only saves time but also reduces the complexity of installation, making it an increasingly popular choice among professionals and DIY enthusiasts alike. Understanding how to use press fitting systems is essential for achieving efficient and durable results.
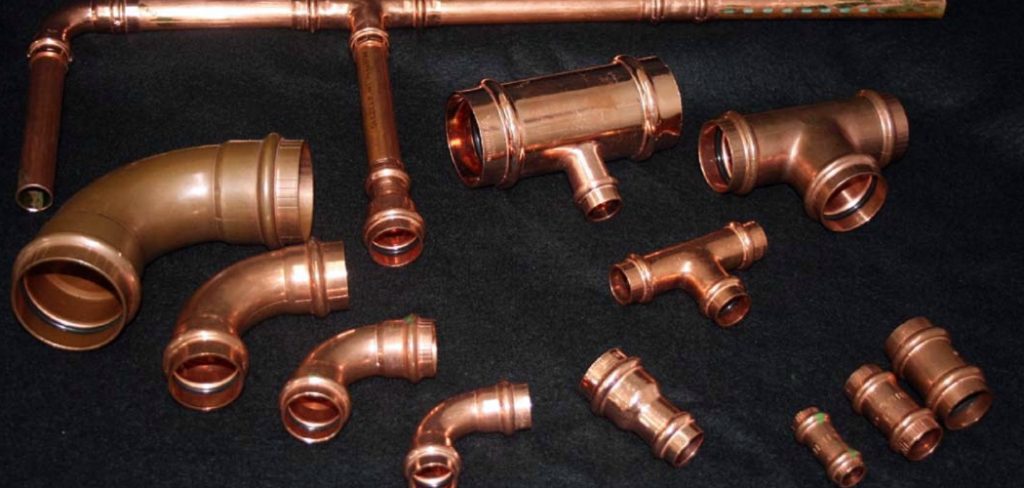
What Are Press Fitting Systems?
Press fitting systems are advanced piping connection solutions designed to simplify and streamline the installation process. These systems consist of pipes and fittings that are joined using a press tool, which mechanically secures the connection by compressing a specially designed fitting around the pipe. The fittings typically feature seals or O-rings to ensure a watertight or airtight connection, making them highly effective for various applications, including plumbing, heating, and gas systems.
Their versatility, ease of use, and reliability make press fitting systems a preferred alternative to traditional methods like soldering or threading. Additionally, they are compatible with various materials, such as copper, stainless steel, and PEX, further enhancing their adaptability to different project requirements.
Key Benefits of Press Fitting Systems
Press fitting systems offer several advantages that make them an ideal choice for various types of pipe installations:
Time-Saving Installation
The press fitting process is significantly faster compared to traditional methods like soldering or welding. With minimal preparation required, connections can be completed in a matter of seconds.
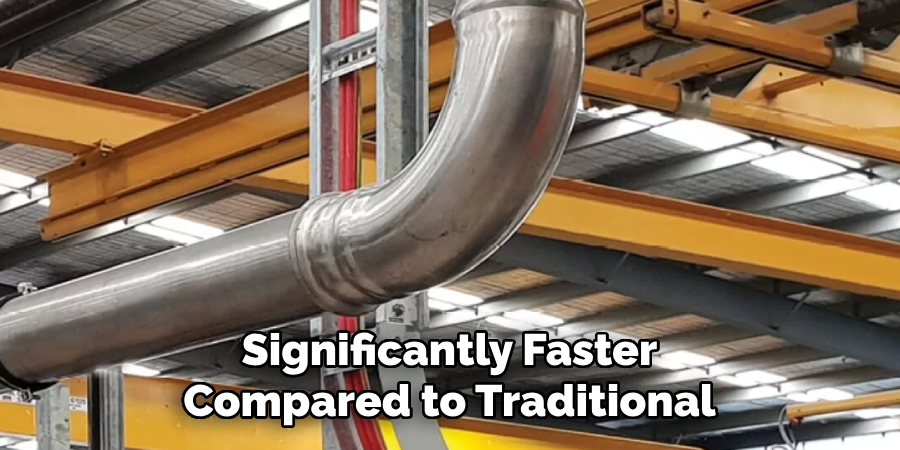
Enhanced Safety
By eliminating the need for open flames or hot work, press fitting reduces the risk of fire and other hazards often associated with soldering or welding.
Reliability and Durability
Press fittings create secure, leak-proof seals, ensuring long-lasting connections under a wide range of conditions, including high pressure and temperature variations.
Ease of Use
Thanks to their simple design, press fitting systems are easy to handle and require minimal training, making them accessible to both professionals and DIY users.
Versatility
Press fitting systems are compatible with various pipe materials, including copper, stainless steel, and PEX, making them suitable for plumbing, heating, and gas applications.
Cost-Effectiveness
By streamlining the installation process and reducing the need for specialized tools or skilled labor, press fitting systems help save both time and money.
These key benefits underscore why press fitting systems are rapidly becoming a preferred solution for modern pipe installations.
Tools and Materials Needed
To successfully use press fitting systems, it is essential to have the right tools and materials on hand. Below is a list of the key items required for a smooth and efficient installation:
Press Tool
The press tool is the primary piece of equipment needed for creating secure connections. These tools are available in manual, battery-powered, or hydraulic options, depending on the scope and scale of the project.
Press Jaws or Attachments
Press tools are equipped with interchangeable jaws or attachments designed to fit various pipe sizes and fittings. Ensure the correct size is selected for the specific application to achieve proper compression.
Pipes
The pipes used in press fitting systems must be compatible with the chosen fittings, such as copper, stainless steel, or PEX. Verify the material and size specifications before starting the installation.
Press Fittings
Press fittings, which include seals or O-rings, are specifically designed to work with press tools. These fittings must match the pipe material and size to ensure a leak-proof connection.
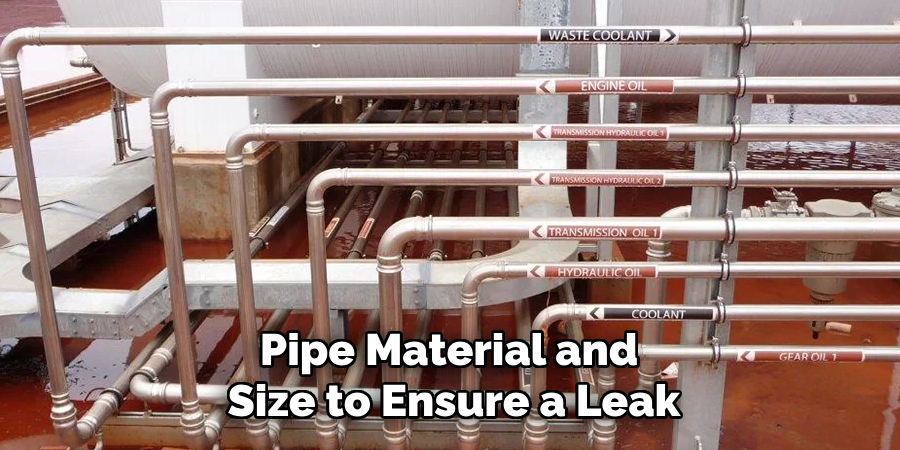
Pipe Cutter
A pipe cutter is essential for cutting pipes cleanly and accurately to the required lengths. Smooth, even cuts are critical for ensuring a proper fit within the press fittings.
Deburring Tool
After cutting the pipes, a deburring tool is used to clean and smooth the edges, removing any burrs or roughness that could damage the fitting seals or compromise the connection.
Marking Tool
A marking tool, such as a permanent marker, is used to indicate the insertion depth of the pipe into the fitting. This helps ensure a proper fit and consistent connections throughout the installation.
10 Methods How to Use Press Fitting Systems
1. Choose the Right Fittings and Pipes
The first step in using a press fitting system is selecting compatible fittings and pipes. Ensure that the fittings match the pipe material, whether it is copper, stainless steel, PEX, or carbon steel. Check the manufacturer’s specifications for size, pressure rating, and application compatibility. Proper selection reduces the risk of system failure and ensures long-term performance.
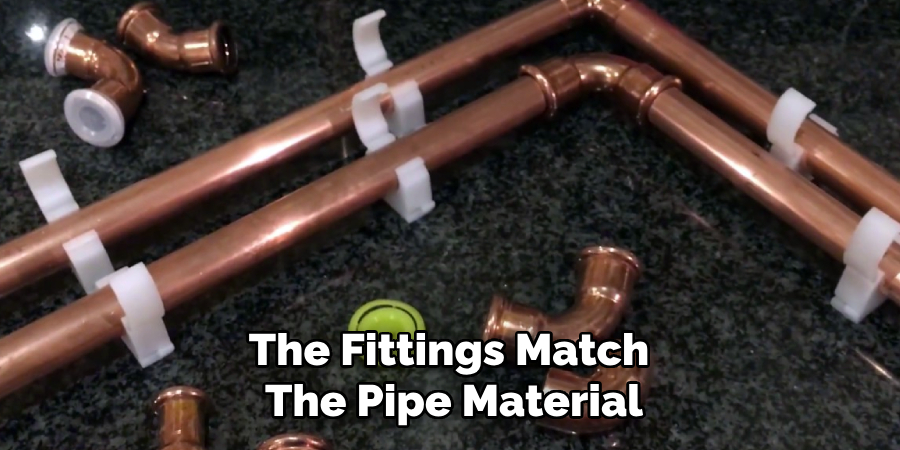
2. Inspect and Prepare the Pipes
Before assembly, inspect the pipes for any damage, such as dents or scratches, that may compromise the seal. Use a pipe cutter to cut the pipe to the required length, ensuring a clean and square cut. Avoid using saws, as they can leave burrs. Deburr the cut edges with a deburring tool to ensure a smooth surface that won’t damage the fitting’s sealing element.
3. Mark the Insertion Depth
Proper insertion depth is crucial for creating a secure and leak-proof connection. Use a depth gauge or the manufacturer’s guidelines to mark the pipe’s insertion depth. Marking ensures that the pipe is inserted fully into the fitting, aligning the sealing elements correctly and preventing leaks or joint failure.
4. Inspect the Fitting
Before inserting the pipe, inspect the fitting for any defects or damage. Check the sealing element, such as an O-ring, for cracks, debris, or misalignment. A damaged or misaligned seal can compromise the joint’s integrity. Replace any defective fittings to ensure a reliable connection.
5. Insert the Pipe into the Fitting
Align the pipe with the fitting and insert it until it reaches the marked insertion depth. Push the pipe straight into the fitting without twisting or angling it. Twisting can dislodge or damage the sealing element, while improper alignment can result in a weak joint. Ensure that the pipe and fitting are properly aligned for a secure connection.
6. Select the Appropriate Press Tool and Jaws
Choose a press tool and jaw size compatible with the pipe and fitting. Modern press tools are available in manual, battery-operated, and hydraulic models. Ensure the jaws match the fitting’s profile to avoid deforming the fitting or compromising the seal. Regularly inspect and maintain the press tool to ensure consistent performance.
7. Position the Press Tool Correctly
Place the press tool’s jaws around the fitting’s designated pressing area. Ensure that the jaws are centered and perpendicular to the fitting. Misalignment during pressing can cause uneven compression, leading to leaks or a weakened joint. Double-check the placement before activating the press tool.
8. Activate the Press Tool
Follow the manufacturer’s instructions to activate the press tool. For battery-operated or hydraulic models, press the trigger or operate the controls to initiate the pressing process. For manual tools, apply steady pressure to complete the press. Allow the tool to complete its cycle fully before removing it to ensure a uniform and secure press.
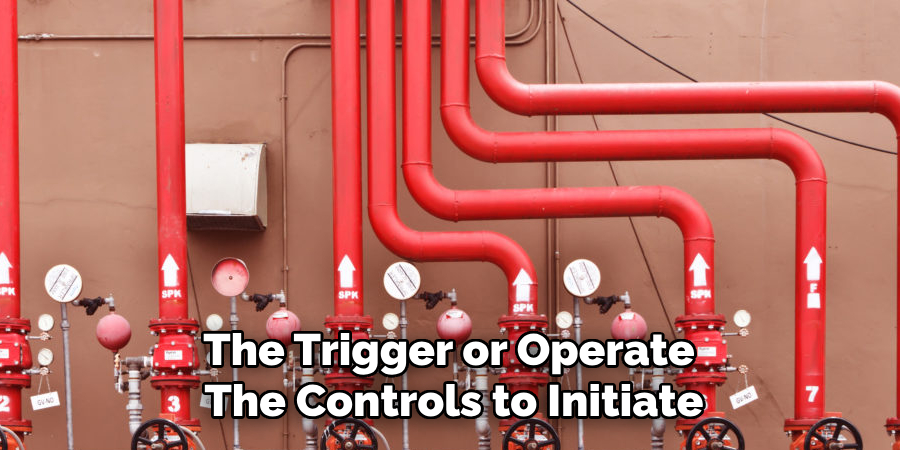
9. Inspect the Completed Joint
After pressing, inspect the joint to ensure it meets quality standards. Check for uniform compression around the fitting and verify that the pipe is still inserted to the correct depth. Look for any visible damage, such as cracks or deformation, that may indicate improper pressing. Conduct a pressure test to confirm the joint’s integrity and leak resistance.
10. Perform Routine Maintenance and Training
To ensure long-term success with press fitting systems, perform regular maintenance on your tools and equipment. Clean and lubricate the press tool as recommended by the manufacturer, and replace worn or damaged jaws promptly. Provide ongoing training for technicians to keep them updated on best practices, tool usage, and safety protocols. Well-maintained tools and knowledgeable technicians contribute to efficient and reliable installations.
Maintenance and Upkeep
Proper maintenance and upkeep of press fitting systems and their associated tools are essential for ensuring optimal performance, safety, and longevity. Below are key practices to maintain the system and equipment effectively:
1. Clean and Inspect Tools Regularly
Press tools, jaws, and other equipment should be cleaned after each use to remove debris, dirt, or grease that can affect their operation. Inspect the tools regularly for signs of wear, damage, or misalignment. Addressing these issues promptly prevents further equipment failure and ensures consistent pressing quality.
2. Replace Worn or Damaged Components
Components such as press tool jaws, O-rings, and sealing elements may wear out over time. Replace any worn, damaged, or defective parts immediately to maintain the reliability of the connections and prevent leaks.
3. Lubricate Moving Parts
Follow the manufacturer’s recommendations to lubricate moving parts of the press tool. Proper lubrication reduces friction, prevents unnecessary wear, and keeps the tool functioning smoothly.
4. Calibrate Press Tools
Periodically, press tools should be calibrated to ensure consistent performance. Check with the manufacturer for calibration schedules and procedures. Accurate calibration guarantees that the press force applied meets the required specifications for secure joints.
Conclusion
Using press fitting systems effectively requires careful preparation, attention to detail, and adherence to best practices. By following these ten methods, you can achieve secure, leak-proof connections that meet the highest standards of quality and reliability. Now that you know how to use press fitting systems, try it yourself today and feel good about completing such a big DIY job!